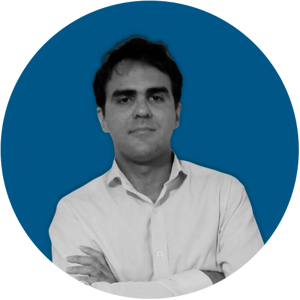
Opinião
Titanium Pull-in Tube: uma solução submarina imune à corrosão sob tensão por CO2
A utilização de sistemas de coleta baseada em dutos flexíveis sempre foi uma característica dos projetos submarinos da Petrobras. Desde o início da produção na Bacia de Campos, a Petrobras tem utilizado extensivamente dutos flexíveis para explotação de hidrocarbonetos.
Com a descoberta dos primeiros campos de petróleo do pré-sal, a decisão técnica pela utilização de tubos flexíveis submarinos para a produção ocorreu de forma natural. Ainda que um grande programa de qualificação tenha sido desenvolvido em conjunto com os diversos fabricantes, em 2016 um novo e inédito modo de falha na indústria foi identificado em dutos flexíveis que transportam fluidos com alto teor de CO2 sob alta pressão. A chamada corrosão sob tensão por CO2 (Stress Corrosion Cracking due CO2) se apresentou como um desafio para as atividades de produção desempenhadas pela Petrobras no pré-sal. O fenômeno pode ser observado tanto no trecho de duto suspenso, entre a plataforma e o leito marinho (riser), quanto no trecho de duto posicionado no solo (flowline). Portanto, o gerenciamento da integridade destes dutos passou a demandar uma atenção especial das áreas técnicas e levaram ao aumento de inspeções nas fases de operação.
Com o desafio de desenvolver um novo projeto de dutos flexíveis capaz de eliminar a falha por SCC CO2, a Petrobras passou a optar pela utilização de uma arquitetura submarina baseada em dutos rígidos nos projetos de desenvolvimento da produção que apresentassem algum risco de ocorrência do fenômeno. Porém, mesmo que os dutos rígidos submarinos pudessem ser construídos de forma mais fácil com metalurgia imune à corrosão e ao SCC CO2, o maior desafio era sua aplicação em projetos complementares e manutenções de campos maduros, onde as plataformas já se encontravam construídas. Vale lembrar que a Petrobras utiliza sistemas de conexão entre riser e plataforma diferentes para dutos rígidos e flexíveis. Os chamados I-Tubes (figura 1), estruturas tubulares montadas no costado dos FPSO, são os sistemas de interface padrão para receber dutos flexíveis nas unidades de produção. Estes possuem um pequeno desvio angular que é facilmente acomodável para dutos flexíveis, mas não permitem a passagem de dutos rígidos em seu interior.
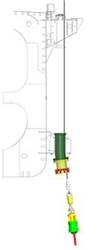
Figura 1 – Operação de montagem de um riser em um I-tube na embarcação
Como solução, a Petrobras trabalhou em um novo componente montado no topo dos dutos rígidos que viabiliza sua montagem em suportes tipo I-tube. O Titanium Pull-in Tube (TiPT) foi desenvolvido pela Petrobras utilizando o conceito das Stress Joints de titânio, amplamente aplicadas em projetos de dutos rígidos offshore ao redor do mundo. O TiPT é composto por um conjunto de tubos fabricados em titânio (grau 29) e um capacete adaptador semelhante ao utilizado na conexão de risers flexíveis nos I-Tubes. Dois destes tubos possuem um formato cônico (stress joints), e são montados conforme as figuras 2 e 3. A stress joint superior permite a acomodação do tubo no interior do I-tube atendendo aos critérios de projeto, enquanto a stress joint inferior absorve os esforços impostos pelo riser. O titânio foi selecionado pela sua alta resistência à corrosão e imunidade ao SCC CO2. Além disso, sua alta resistência mecânica e alta flexibilidade tornam o equipamento compacto e fácil de instalar, viabilizando sua implantação nas unidades existentes e originalmente concebidas com sistemas de suportação e demais interfaces voltadas aos dutos flexíveis.
O TiPT foi desenvolvido inteiramente pela Petrobras, em uma parceria entre engenharia submarina e o centro de pesquisas da Petrobras, e patenteado após um intenso estudo de viabilidade técnica. O equipamento foi pensado para dispensar obras nas plataformas. O contato direto com o mercado de potenciais fornecedores e instaladores permitiu uma avaliação do interesse e capacidade de fornecimento, além de verificar eventuais dificuldades técnicas de fabricação e instalação.
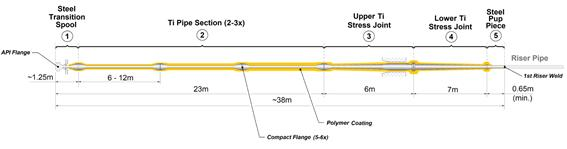
Figura 2 – Arranjo de um Titanium Pull in Tube
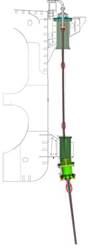
Figura 3 – TiPT montado no interior de um I-tube
Atualmente, a Petrobras possui uma alternativa imune ao SCC CO2 aplicável às unidades em operação. Sua aplicação é possível tanto em projetos complementares, quanto em projetos de substituição de dutos flexíveis já em operação. Os ganhos com a utilização da nova tecnologia vão muito além do aumento da segurança operacional, contemplando redução de custos e melhoria da eficiência operacional. O gerenciamento da integridade dos dutos sob risco de SCC CO2 requer inspeções periódicas, eventuais paradas de produção para testes e, em casos extremos, pode exigir a troca do duto flexível. O TiPT, além de eliminar os custos de substituição de risers e inspeções periódicas, também dispensa paradas de produção para testes de integridade.
O projeto WAG Full Field Tupi, desenvolvido em parceria com a Shell e a Petrogal, foi selecionado como piloto da tecnologia. Seu escopo corresponde à conversão de 15 poços de injeção de água do campo de Tupi em poços injetores de água e gás (WAG – Water Alternating Gas) por meio da instalação de aproximadamente 98 km de dutos rígidos de injeção de gás. A conexão destes poços depende da interligação de 11 risers novos nas unidades: P-66, P-67, P-69, FPSO Cidade de Maricá e FPSO Cidade de Saquarema. Todos os risers utilizam o Titanium Pull-in Tube como interface entre dutos e plataformas. O início da implantação deste projeto de investimento está programado para o final de 2023. Com sua implantação, estima-se um significativo acréscimo de produção em Tupi devido ao melhor gerenciamento do gás reinjetado, maximizando os benefícios trazidos por este para o fator de recuperação final do campo.
Estimativas indicam que a utilização do TiPT pode levar a uma economia de até US$ 200 milhões com custos de gerenciamento da integridade destes dutos somente neste projeto.
Raphael Moreira de Brito é engenheiro de Projetos de Sistemas Submarinos de Produção da Petrobras.
Fabio Rocha Hoelz é engenheiro de Equipamentos Submarinos da Petrobras.
Ludimar Lima de Aguiar é consultor em Tecnologia de Risers Rígidos da Petrobras.